How Manufacturers Can Prepare for Impact of Tariffs
Adjust Financial Forecasts and Seek Domestic Raw Material Sources
Key Takeaways:
- Tariffs on steel and aluminum are making it more important than ever to explore new suppliers and refine costs.
- Adjusting your 2025 forecasts now allows you to confidently manage staffing, pricing and growth as trade policies evolve.
- Staying informed on potential tax advantages can help offset increased costs and support a brighter path forward for your business.
Worldwide tariffs introduced in early 2025 are reshaping the manufacturing sector, creating both challenges and opportunities. For companies that act swiftly, there’s a chance to adapt supply chains, refine financial strategies and maintain competitiveness. Whether your business imports raw materials or exports finished goods, understanding and preparing for these changes can help you stay ahead in a shifting economic environment.
For our Kansas and Arkansas manufacturing clients, the most significant impact is being felt from the tariffs on steel and aluminum. Manufacturing industries such as aerospace, equipment, metal fabrication and farm machinery are expected to experience particularly significant impacts, if they haven’t already.
Tariff Timeline
The rollout of tariffs is ongoing, with updates still emerging as the U.S. evaluates its trade policies. Here’s what’s in place as of March 21, 2025:
- China – Tariffs of up to 25% on most goods, 50% on specific categories and 100% on electric vehicles, effective Feb. 4, 2025.
- Mexico – Tariffs of up to 25% on all products were imposed as of March 4, 2025. However, tariffs on goods covered by the U.S. Mexico Canada Agreement (USMCA), including automobiles, are delayed until April 2, 2025.
- Canada – Tariffs of 10% on energy resources and 25% on other products started March 4, 2025, with USMCA-covered goods delayed until April 2, 2025.
- Worldwide – Tariffs of 25% on steel and aluminum imports from all countries took effect March 12, 2025.
Additional tariffs on other goods are under consideration as part of ongoing trade reviews, including the America First Trade Policy and the Fair and Reciprocal Plan.
Steel and Aluminum
The U.S. steel industry is well-positioned to increase production, offering a potential domestic alternative for manufacturers reliant on imported steel. Aluminum, however, presents a different scenario. The U.S. imports 2.7 million metric tons of aluminum annually from Canada—60% to 75% of its consumption—while domestic production capacity remains limited.
Expanding U.S. aluminum output would require importing bauxite, the primary raw material, largely from Australia, which produces about 25% of the global supply. Potential costs, including transportation and possible retaliatory tariffs, could complicate this shift. With only about a dozen U.S. aluminum facilities—three of which are currently idle—domestic supply growth may take time.
Strategies to Adapt to Tariff Changes
Manufacturers dependent on imported steel and aluminum can take proactive steps to manage rising costs and maintain stability:
- Supply chain – Map out where your steel and aluminum originate to identify vulnerabilities and opportunities. Build relationships with multiple vendors.
- Domestic suppliers – Explore U.S. suppliers for raw materials. While demand for domestic steel and aluminum is surging, new capacity may emerge as producers respond to the market. Persistence could pay off. If domestic suppliers are not available, explore tariff-free countries to find cost-effective alternatives.
- Financial forecasting – Update your 2025 forecasts to reflect tariff-related cost increases. Compare the expense of imported goods with potential domestic options and adjust pricing, workforce plans, and cash flow projections accordingly.
- Cost management – Review expenses beyond raw materials. Trimming discretionary spending now could provide flexibility if economic conditions tighten. Renegotiate supplier contracts to secure stable pricing.
- Hold off on big investments – Did you plan an expansion or purchase of new equipment in 2025? Consider putting it on hold until the economic outlook is more stable.
- Stay informed about tariffs – Monitor tariff developments closely. Changes could open new possibilities or require further adjustments to your strategy. Stay abreast of new developments so you can update your financial forecast as needed. Accurate forecasts will help you adjust plans for adding to your workforce, upgrading equipment or expanding to new markets.
- Talk to your tax advisor – Some tax rules that are important to manufacturers are scheduled to expire this year, or have already begun phasing out. Bonus depreciation has declined to 40% for purchases made in 2025, and despite much anticipation, research and development expensing has not yet been reinstated. Your tax advisor may be able to identify tax-advantaged strategies to help you ride out the tariff war.
Moving Forward
The tariff landscape is evolving quickly, and its full impact will unfold over time. For now, preparation is key. Contact an Adams Brown manufacturing advisor to explore how these changes affect your business and to develop a tailored plan.
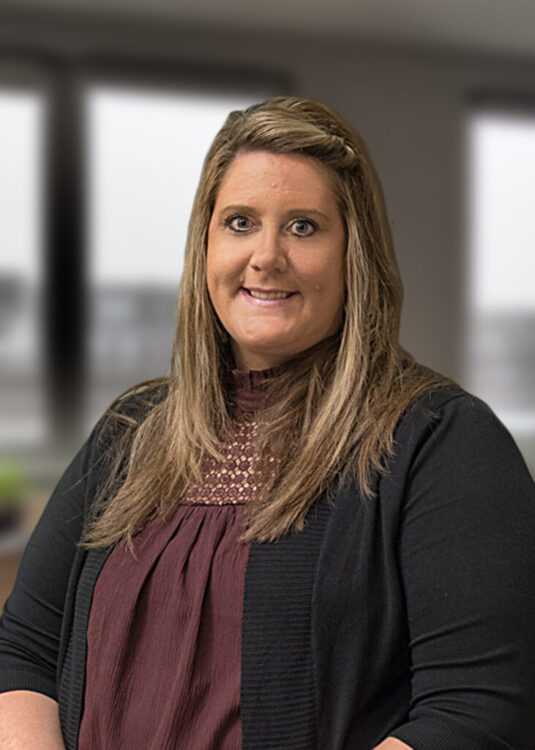